Work Hours
Monday to Friday: 7AM - 7PM
Weekend: 10AM - 5PM
【Practical】Reliability Design of Inverter
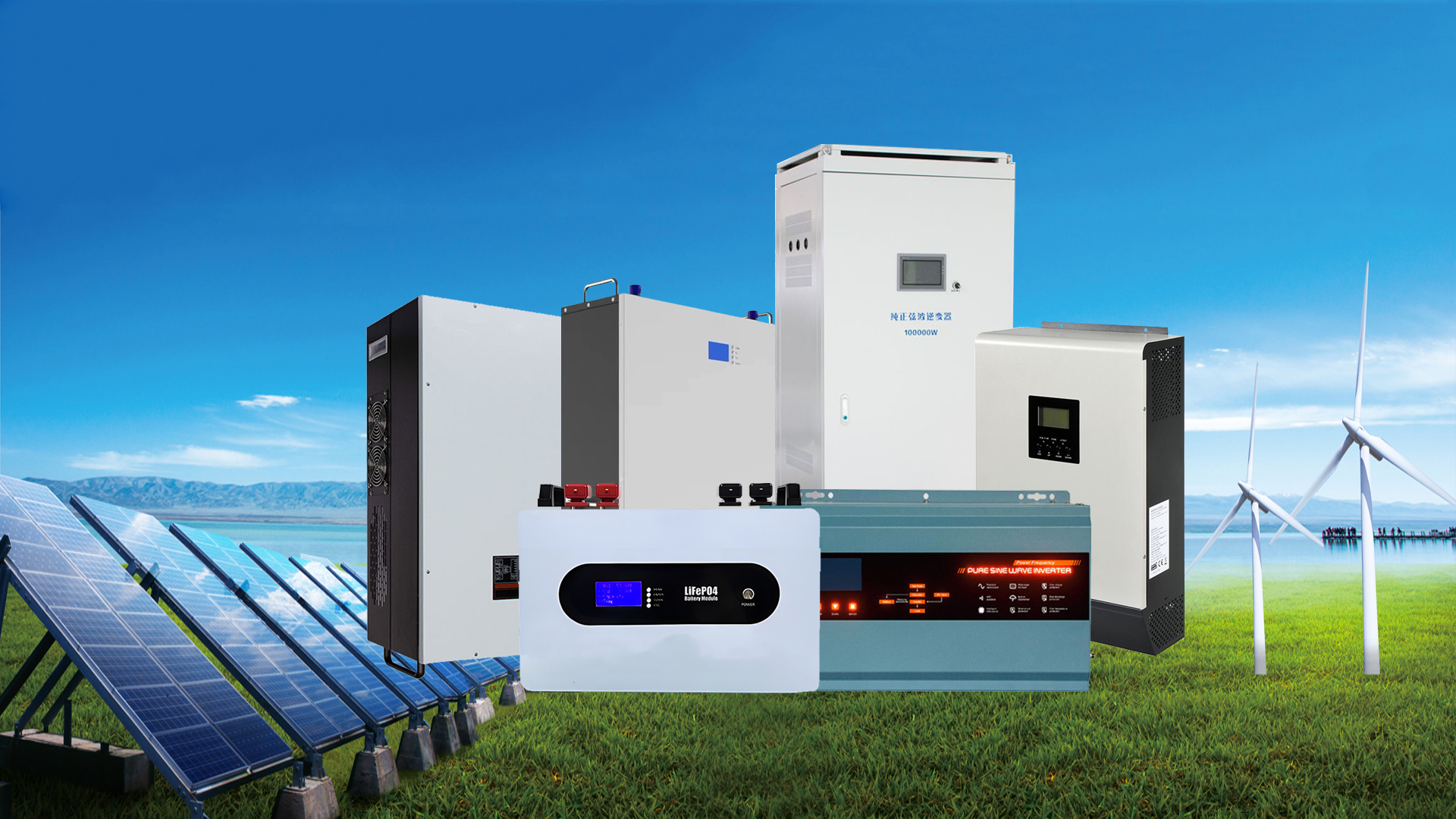
Whether it is a micro inverter, a string inverter, or a large photovoltaic grid-connected inverter, it is composed of semiconductor modules, including switching elements and capacitor elements. The reliability of these elements determines the reliability of the photovoltaic inverter. In the grid-connected photovoltaic power generation system, the inverter installation environment is diverse, and it may also be necessary to handle very high power currents in high temperature, high temperature, and salt spray environments. These factors increase the failure rate of the inverter and the reliability of the system.
Topology reliability
To adapt to the on-site environmental conditions of the photovoltaic inverter, the topology of the inverter must be optimized. The design of a reasonable circuit topology is an important factor affecting the reliability of the inverter.
In order to ensure that the bridge arm power switch tube is not directly connected, the power switch tube of the same bridge arm must be set with a dead time, thereby reducing the waveform quality of the grid current. The bridge wall direct connection problem of the traditional bridge-type grid-connected inverter affects the reliability of the grid-connected inverter. The dual-buck half-bridge inverter based on hysteresis current control does not have the direct connection problem of the bridge arm power switch tube of the traditional bridge-type grid-connected inverter, which improves the system reliability. Single-phase Z-source inverter. The inverter can realize step-up and step-down conversion, and there is no problem of bridge arm power switch tube direct conduction, but 2 inductors and 2 capacitors are required to increase the input voltage.
Leakage current is also one of the main factors affecting the reliability of the inverter. Optimizing the circuit topology is the main method to solve the leakage current problem. The three-level dual-Buck full-bridge inverter circuit in the dual-Buck improved version suppresses the leakage current to an almost negligible level, uses a small number of active devices, has a small number of on-state currents flowing through the devices, and has a small number of high-frequency working devices; no voltage equalization control is required. At the same time, through theoretical calculation analysis and comparison, it is shown that the three-level dual-Buck full-bridge inverter circuit in the dual-Buck improved version has high reliability.
The number of components affects circuit reliability
A small number of devices means a simpler structure and control, and a small chance of error. In particular, passive devices have higher reliability than active devices. The power module integrates multiple components and multiple discrete devices into one module, which has a compact structure and reduces the parasitic impedance of the wiring between devices. The power module drive circuit and the main power circuit are led out from different pins, which reduces the electromagnetic interference of the IGBT main power circuit to the drive circuit. The module is equipped with an NTC resistor, which can accurately detect the internal temperature of the module.
Component reliability
The power switch is the most likely location to fail. To evaluate the reliability of the inverter, the reliability of the power switches that make up the inverter must be evaluated. The mean trouble-free working time of the inverter system is mainly affected by the reliability of the switch tube. The reliability of the power switch tube is the key to the reliability of the entire system. Increasing the reliability of the inverter switch element greatly increases the overall reliability of the inverter. Therefore, the selection of high-quality power switch tubes and reducing the electrical stress of the switch tube can effectively improve the reliability of the inverter.
As an electronic product, the inverter uses capacitors as the most basic components. The DC bus support capacitor is mainly used for energy storage and filtering. It has to withstand very high pulse current and pulse voltage, and is one of the components with the shortest life of the inverter. There are two types of DC bus capacitors: aluminum electrolytic capacitors and film capacitors, each with its own advantages. The main advantages of electrolytic capacitors are large monomer capacity and low price, and the advantages of film capacitors are high monomer voltage. There are also the following advantages: the life of electrolytic capacitors is generally 2000~3000 hours, and the long life is 5000~6000 hours, and it is easy to leak; the life of film capacitors is generally more than 100000 hours. Moreover, film capacitors also have a self-healing effect. The withstand voltage of electrolytic capacitors is generally 500-550V, and the withstand voltage of film capacitors is generally 1000-1300V. Film capacitors can withstand the impact of surge voltage twice the rated voltage and can withstand reverse pulse voltage for a long time.
Redundant design
In places where the system or equipment plays a key role in completing the task, add more than one set of functional channels, working elements or components that complete the same function to ensure that when this part fails, the system or equipment can still work normally, so as to reduce the probability of failure of the system or equipment and improve the reliability of the system. After taking redundant measures, the reliability of this system can be greatly improved immediately without changing the internal design. If the failure rate of a single system is 50%, the failure rate can be immediately reduced to 25% after adopting a redundant system.
Triple-proof design
Triple-proof design refers to moisture-proof, salt spray-proof and mildew-proof design. The working environment of the inverter is diverse, and moisture, salt spray and mildew will reduce the insulation strength of the material, cause leakage and short circuit, and thus lead to electronic failure and accidents. Therefore, it is necessary to prevent or reduce the adverse effects of environmental conditions on the reliability of the inverter to ensure the performance of the inverter in operation and increase the reliability of the product in harsh environments.
Outdoor solar inverters fully consider the requirements of triple-proof design. The specific contents of the three-proof treatment include: (1) the surface of the box is treated with acid pickling and phosphating, and then a dense plastic powder layer is electrostatically sprayed. After high-temperature curing, the surface of the box can be effectively protected; (2) a self-clamping rubber sealing ring is used between the cover and the box; (3) the internal control circuit board is sprayed with three-proof paint; (4) the input and output lines are sealed with waterproof terminals, etc.